How does a small business turn around after facing repeated production delays?
Client Profile
A small manufacturing business in Mumbai specializing in high-quality specialty products with tight turnaround demands. The business relied heavily on maintaining timely deliveries to retain its reputation and satisfy its clients.
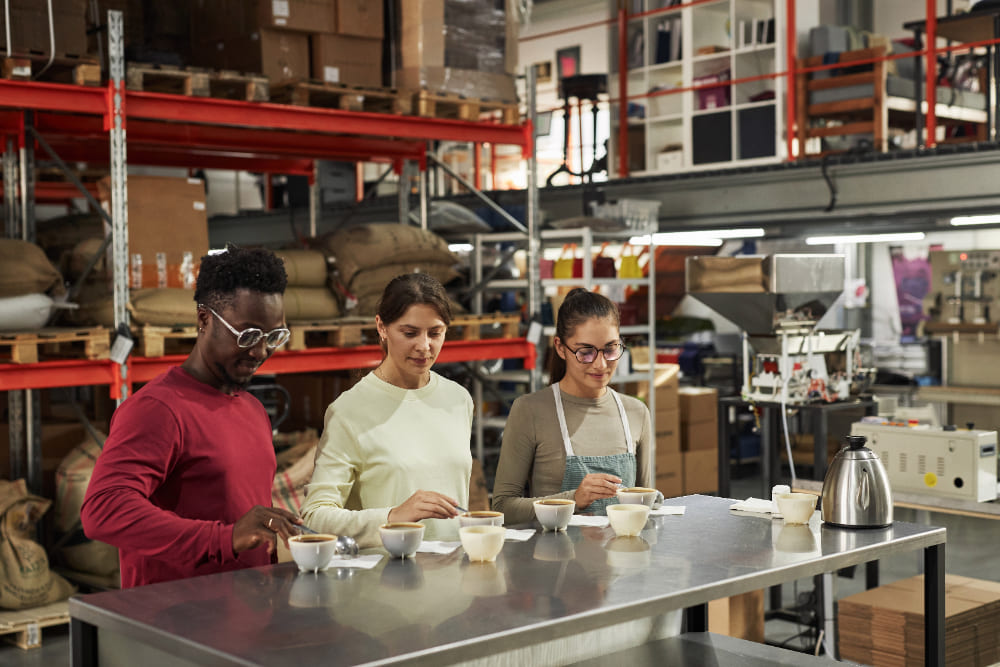
Challenges
Staffing Issues
Insufficiently resourced teams were unable to meet production demands.
Supply Chain Disruptions
Lack of backup suppliers and inefficient tracking systems caused frequent delays.
Operational Weaknesses
Absence of contingency plans meant minor setbacks escalated into major crises, leading to missed deadlines and client dissatisfaction.
Our Approach
Identified Key Operational Bottlenecks
- Conducted interviews and on-site assessments to pinpoint underperforming areas, such as insufficient staffing and supply chain inefficiencies.
Developed a Customized Risk Mitigation Plan
Designed practical solutions, including:
- Backup supplier agreements to ensure material availability.
- Automated tracking systems for real-time updates.
- Cross-training for staff to increase flexibility and maintain workflows during disruptions.
Introduced Regular Monitoring Systems
Established key performance indicators (KPIs) and review checkpoints to detect and address issues proactively.
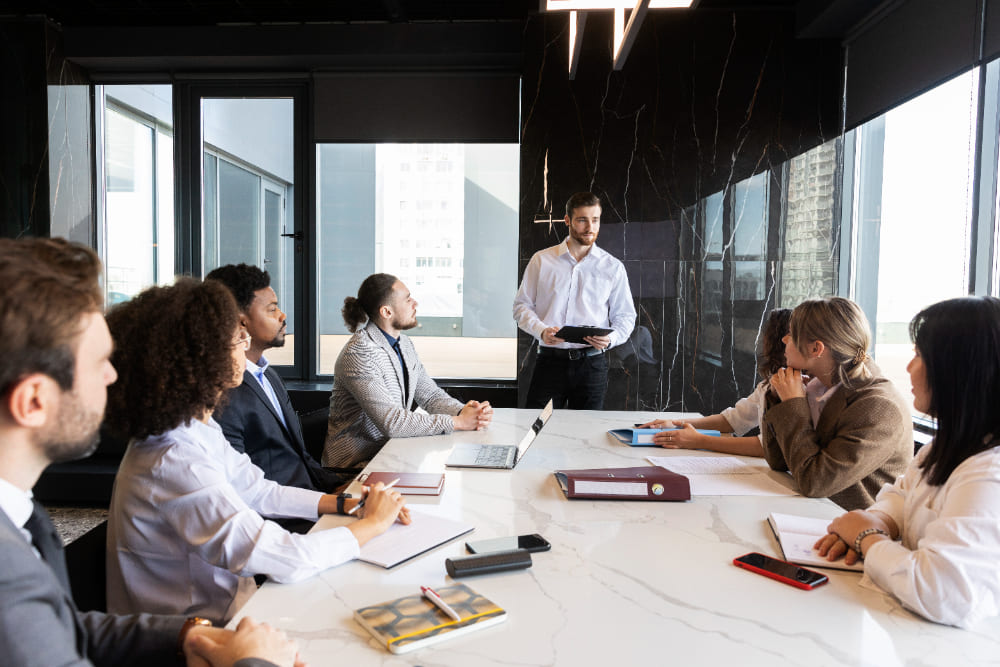
Results
Improved Delivery Timeliness
On-time deliveries increased by 25%, restoring client confidence and satisfaction.
Reduced Complaints
The client saw a significant reduction in customer complaints, bolstering their reputation.
Enhanced Process Control
By gaining better control over operations, the business is now equipped to handle challenges proactively, leading to consistent growth opportunities.